图书介绍
高炉炼铁生产技术手册2025|PDF|Epub|mobi|kindle电子书版本百度云盘下载
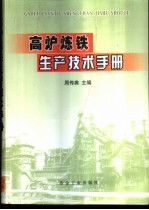
- 周传典主编 著
- 出版社: 北京:冶金工业出版社
- ISBN:750243013X
- 出版时间:2002
- 标注页数:881页
- 文件大小:49MB
- 文件页数:901页
- 主题词:
PDF下载
下载说明
高炉炼铁生产技术手册PDF格式电子书版下载
下载的文件为RAR压缩包。需要使用解压软件进行解压得到PDF格式图书。建议使用BT下载工具Free Download Manager进行下载,简称FDM(免费,没有广告,支持多平台)。本站资源全部打包为BT种子。所以需要使用专业的BT下载软件进行下载。如BitComet qBittorrent uTorrent等BT下载工具。迅雷目前由于本站不是热门资源。不推荐使用!后期资源热门了。安装了迅雷也可以迅雷进行下载!
(文件页数 要大于 标注页数,上中下等多册电子书除外)
注意:本站所有压缩包均有解压码: 点击下载压缩包解压工具
图书目录
1 炼铁原料1
1.1 炼铁精料1
1.1.1 高炉炼铁对精料的要求1
1.1.1.1 提高入炉品位1
1.1.1.2 控制入炉矿的脉石组成和杂质含量2
1.1.1.3 做好入炉料成分稳定的工作4
1.1.1.4 提高入炉料的强度和优化粒度组成5
1.1.1.5 提高入炉料的冶金性能7
1.1.2 高炉炉料结构合理化10
1.1.2.1 几个主要国家高炉炉料结构的特点11
1.1.2.2 我国高炉炉料结构的优化12
1.2 天然块矿13
1.2.1 含铁矿物的分类及铁矿石工业类型的划分13
1.2.2 天然矿石的冶炼性能13
1.2.2.1 强度与粒度组成13
1.2.2.2 热爆裂性能15
1.2.2.3 高温冶金性能16
1.2.3 天然矿石的综合评价17
1.2.4 部分国内与进口天然矿的理化性能17
1.3 烧结矿19
1.3.1 烧结矿矿物组成与显微结构19
1.3.1.1 高碱度烧结矿矿物组成与显微结构24
1.3.1.2 自熔性烧结矿的矿物组成和显微结构25
1.3.1.3 酸性烧结矿矿物组成和结构构造27
1.3.2 烧结矿化学成分与冶金性能的关系28
1.3.2.1 烧结碱度与冶金性能的关系28
1.3.2.2 烧结矿品位、二氧化硅含量与冶金性能的关系30
1.3.2.3 烧结矿氧化亚铁含量与冶金性能的关系30
1.3.2.4 烧结矿中氧化镁、三氧化二铝含量与冶金性能的关系31
1.3.2.5 烧结矿中氟化钙和二氧化钛含量与冶金性能的关系32
1.3.3 改善烧结矿冶金性能的技术措施33
1.3.3.1 烧结精料33
1.3.3.2 原料中和混匀34
1.3.3.3 配料自动化34
1.3.3.4 均匀烧结35
1.3.3.5 烧结过程自动控制35
1.3.3.6 厚料层烧结36
1.3.3.7 低温烧结法36
1.3.3.8 热风烧结37
1.3.3.9 小球烧结与球团烧结法38
1.3.3.10 双层布料、双碱度料烧结与双球烧结39
1.3.3.11 改善入炉烧结矿粒度组成的措施40
1.3.3.12 降低烧结矿低温还原粉化率的措施41
1.3.4 近年来主要重点企业与典型地方骨干企业烧结矿产质量及主要技术经济指标42
1.3.4.1 我国主要重点企业烧结矿产质量及主要技术经济指标42
1.3.4.2 我国典型地方骨干企业烧结矿产质量及主要技术经济指标42
1.3.4.3 日本部分企业烧结矿产质量及主要技术经济指标43
1.3.5 YB/T 421—92铁烧结矿行业标准中的技术要求44
1.4 球团矿45
1.4.1 球团矿矿物组成与显微结构45
1.4.1.1 球团矿的固结45
1.4.1.2 国外几种球团矿的矿物组成47
1.4.1.3 鞍钢氧化镁酸性球团矿矿物组成与结构构造47
1.4.1.4 含硼自熔性球团矿的矿物组成48
1.4.2 球团矿冶金性能及其影响因素49
1.4.2.1 不同品种精矿制造的球团矿的冶金性能49
1.4.2.2 不同焙烧方式对球团矿冶金性能的影响49
1.4.2.3 不同品位商品球团矿的冶金性能50
1.4.2.4 含氧化钙、氧化镁球团矿的冶金性能50
1.4.2.5 球团矿的还原膨胀性能52
1.4.3 提高球团矿质量的技术措施52
1.4.3.1 球团矿生产对铁精矿和熔剂添加剂质量的要求52
1.4.3.2 黏结剂品种与质量52
1.4.3.3 酸性球团矿质量的优化53
1.4.3.4 焙烧过程均匀化与质量的严格控制54
1.4.3.5 多孔球团与破碎球团54
1.4.3.6 内燃球团矿55
1.4.4 近年来我国主要带式机、链箅机—回转窑、竖炉球团厂产质量及主要技术经济指标55
1.4.5 部分国外及进口球团矿理化性能57
1.4.6 部分国内外球团矿质量标准58
1.5 原料的理化与冶金性能及检测方法59
1.5.1 常规化学成分59
1.5.2 其他元素59
1.5.3 粒度组成59
1.5.4 物理性能60
1.5.5 特殊检验60
1.5.6 冶金性能检测60
1.5.6.1 转鼓强度检测60
1.5.6.2 落下指数61
1.5.6.3 抗压强度61
1.5.6.4 贮存强度61
1.5.6.5 热爆裂性能61
1.5.6.6 低温还原粉化性能62
1.5.6.7 还原性能62
1.5.6.8 铁矿球团还原膨胀性能63
1.5.6.9 荷重还原软化性能和熔滴性能63
1.6 熔剂64
1.6.1 石灰石64
1.6.2 白云石、菱镁石和蛇纹石65
1.6.3 硅石66
1.6.4 转炉钢渣66
1.7 辅助原料68
1.7.1 碎铁68
1.7.2 轧钢皮与均热炉渣68
1.7.3 天然锰矿石68
1.7.4 萤石69
1.7.5 钛渣及含钛原料69
参考文献70
2 高炉燃料72
2.1 焦炭72
2.1.1 高炉焦炭的理化性质72
2.1.1.1 高炉焦炭的结构性质72
2.1.1.2 焦炭分析74
2.1.1.3 焦炭的化学性质76
2.1.1.4 焦炭的物理性质77
2.1.1.5 焦炭机械强度81
2.1.1.6 焦炭力学性质82
2.1.1.7 其他84
2.1.2 高炉冶炼对焦炭质量的要求85
2.1.2.1 焦炭在高炉内的变化85
2.1.2.2 高炉冶炼对焦炭质量的要求86
2.1.3 提高焦炭质量的措施89
2.1.4 焦炭质量与经济效益92
2.2 煤粉92
2.2.1 高炉喷吹用煤的工艺性能92
2.2.1.1 煤的孔隙率92
2.2.1.2 煤的比表面积93
2.2.1.3 煤的可磨性93
2.2.1.4 煤的着火温度93
2.2.1.5 煤灰熔融性93
2.2.1.6 胶质层厚度 Y 值94
2.2.1.7 煤的 CO2反应性94
2.2.1.8 煤粉的流动性94
2.2.1.9 煤的细度(粒度)94
2.2.1.10 煤粉爆炸性96
2.2.2 高炉对喷吹煤的性能要求97
2.3 气体燃料98
参考文献99
3 高炉冶炼的基本理论101
3.1 炉料还原过程101
3.1.1 铁氧化物还原热力学102
3.1.2 铁氧化物还原的动力学105
3.1.2.1 还原机理105
3.1.2.2 还原反应速度105
3.1.2.3 影响铁矿石还原的因素106
3.1.3 直接还原度及其发展程度对还原剂消耗量的影响107
3.1.3.1 直接还原度107
3.1.3.2 直接及间接还原发展程度及对还原剂消耗的影响109
3.1.4 非铁元素的还原109
3.1.4.1 硅109
3.1.4.2 锰111
3.1.4.3 磷112
3.1.4.4 硫112
3.1.4.5 其他元素113
3.1.5 铁中渗碳过程及生铁的形成115
3.2 炉料在高温下的性状变化及造渣过程116
3.2.1 炉料的分解与挥发116
3.2.1.1 炉料的水分蒸发与水化物分解116
3.2.1.2 燃料中挥发分的逸出116
3.2.1.3 碳酸盐分解116
3.2.1.4 其他物质的挥发117
3.2.2 炉料的高温性状变化及软熔滴落过程117
3.2.3 造渣过程及炉渣性能118
3.2.3.1 高炉的造渣过程118
3.2.3.2 成渣过程对高炉冶炼的影响119
3.2.3.3 炉渣结构及矿物组成119
3.2.3.4 高炉渣的物理性质及其影响因素121
3.2.3.5 炉渣的化学性质127
3.3 高炉内的煤气、炉料及渣铁的运动127
3.3.1 料柱中煤气流的运动128
3.3.1.1 料柱的多孔介质特性128
3.3.1.2 煤气在料柱中运动的阻力损失130
3.3.1.3 煤气在块状带中的流动特点及影响因素132
3.3.1.4 煤气在软熔带和滴落带的流动134
3.3.1.5 煤气在高炉内的流动与分布的理论解析136
3.3.2 炉料分布与下降运动142
3.3.2.1 炉料落点位置及轨迹计算142
3.3.2.2 炉料的堆角146
3.3.2.3 炉料粒度的径向分布148
3.3.2.4 混合料区的形成与焦炭料层的崩塌现象149
3.3.2.5 炉料的下降与流化150
3.3.3 高炉内的渣铁液体运动153
3.3.3.1 渣铁液体在滴落时液泛现象和流化现象153
3.3.3.2 渣铁液滴的滴下运动154
3.3.3.3 炉缸中的渣铁运动157
3.4 高炉内的热量传递与平衡158
3.4.1 风口前燃料燃烧及理论燃烧温度158
3.4.2 高炉内的热交换过程159
3.4.3 高炉内的热量平衡与利用161
3.5 高炉冶炼过程计算机控制与数学模型163
3.5.1 高炉过程计算机控制系统的功能与结构163
3.5.1.1 计算机系统功能与配置163
3.5.1.2 数学模型的发展与建立165
3.5.1.3 计算机控制对检测信息的要求171
3.5.2 高炉中长期控制的模拟模型174
3.5.2.1 Rist 操作线174
3.5.2.2 碳比—直接还原度模型177
3.5.2.3 软熔带模型177
3.5.2.4 高炉炉缸炉底侵蚀线推定模型181
3.5.3 高炉短期控制的数学模型183
3.5.3.1 炉热指数模型183
3.5.3.2 含硅量预报模型184
3.5.3.3 布料控制模型185
3.6 高炉过程的人工智能控制和专家系统188
3.6.1 人工智能技术和专家系统在高炉上的应用188
3.6.1.1 概况188
3.6.1.2 专家系统控制的基本方式190
3.6.1.3 高炉 ES 系统的构成192
3.6.2 炉况诊断与评价 ES 系统193
3.6.3 炉况顺行及异常预报与控制 ES 系统198
3.6.4 炉热监测和控制 ES 系统200
3.6.5 炉顶布料控制的 AI 系统203
3.6.6 出铁操作指导 ES 系统205
3.6.7 大型高炉(武钢4号)专家系统应用实例简介207
3.6.7.1 高炉热状态控制207
3.6.7.2 对高炉操作炉型的管理208
3.6.7.3 专家系统的顺行控制209
3.6.7.4 对炉缸平衡的管理210
3.6.8 在小型高炉(300m3级)上过程监控系统的应用实例介绍210
参考文献214
4 高炉炉体结构及维护217
4.1 高炉炉顶装料设备217
4.1.1 钟式装料设备220
4.1.1.1 固定受料斗220
4.1.1.2 布料器220
4.1.1.3 小钟及小料斗223
4.1.1.4 大钟及大料斗224
4.1.1.5 大小钟传动226
4.1.1.6 均压设施230
4.1.1.7 可调炉喉231
4.1.2 无钟装料设备231
4.1.2.1 并罐式无料钟炉顶232
4.1.2.2 串罐式无料钟炉顶237
4.2 高炉内型242
4.2.1 高炉内型计算242
4.2.1.1 高炉内型尺寸符号242
4.2.1.2 高炉内型各部尺寸间的关系242
4.2.1.3 内型设计不合理影响高炉冶炼的例子245
4.2.2 高炉内型演化245
4.2.3 合理的高炉内型248
4.2.3.1 合理的高炉内型原则248
4.2.3.2 合理的高炉内型各部位尺寸关系248
4.3 高炉炉体内衬结构249
4.3.1 高炉对耐火材料的基本要求249
4.3.1.1 高炉内衬的基本要求249
4.3.1.2 高炉常用耐火材料理化性能249
4.3.1.3 特种耐火材料250
4.3.2 高炉耐火材料的技术要求和选择原则252
4.3.2.1 高炉耐火材料的技术要求252
4.3.2.2 高炉耐火材料选择原则252
4.3.2.3 高炉各部耐火材料的选择252
4.3.3 高炉内衬耐火砖结构253
4.3.3.1 20世纪80年代高炉内衬结构253
4.3.3.2 砌砖厚度256
4.3.3.3 20世纪90年代以后高炉内衬结构257
4.3.4 高炉炉体耐火砖的砌筑258
4.3.4.1 炉体耐火砖衬标准砖型砌筑258
4.3.4.2 非标准砖型砌筑258
4.3.4.3 炉体砌筑的注意事项261
4.4 高炉炉体冷却设备结构262
4.4.1 高炉冷却设备262
4.4.1.1 高炉冷却结构的基本要求262
4.4.1.2 冷却设备的种类262
4.4.1.3 常用冷却设备性能263
4.4.1.4 各种冷却壁的使用部位及作用265
4.4.1.5 铜冷却壁266
4.4.1.6 冷却壁材质269
4.4.1.7 冷却壁水管防渗碳269
4.4.2 冷却设备结构选择269
4.4.2.1 冷却壁几何尺寸270
4.4.2.2 冷却壁传热计算270
4.4.2.3 冷却设备结构选择271
4.4.3 合理冷却结构273
4.4.3.1 合理冷却结构的条件273
4.4.3.2 国外高炉冷却结构273
4.4.4 建议采用的冷却结构275
4.4.5 高炉炉体冷却方式276
4.4.5.1 高炉冷却水质要求276
4.4.5.2 工业水冷却277
4.4.5.3 炉底冷却281
4.4.5.4 汽化冷却282
4.4.5.5 软水闭路循环冷却284
4.4.5.6 武钢5号高炉软水闭路循环冷却287
4.4.5.7 炉壳喷水冷却290
4.4.6 高炉合理用水291
4.4.6.1 选用合理的冷却型式291
4.4.6.2 选择合理的用水方法291
4.5 炉体维护292
4.5.1 建立完善的监控设施292
4.5.1.1 高炉冷却水水温差监测292
4.5.1.2 高炉各部温度监测292
4.5.1.3 高炉各部热流强度监测293
4.5.1.4 冷却壁破损监测295
4.5.1.5 冷却壁水管结垢监测295
4.5.1.6 高炉内衬侵蚀监测296
4.5.2 加强高炉操作,控制边缘气流300
4.5.3 炉体灌浆和压入泥料302
4.5.3.1 灌浆及压入所用泥料302
4.5.3.2 灌浆孔和压入孔304
4.5.3.3 灌浆和压入机械304
4.5.3.4 高压喷灌造衬机305
4.5.4 炉衬喷补306
4.5.4.1 喷补料306
4.5.4.2 喷补装置310
4.5.5 含钛矿护炉310
4.5.5.1 含钛炉料护炉原理310
4.5.5.2 含钛矿加入方法及其用量311
参考文献312
5 高炉冶炼操作313
5.1 高炉操作制度313
5.1.1 送风制度313
5.1.1.1 正确选择风速或鼓风动能313
5.1.1.2 控制适宜的理论燃烧温度321
5.1.1.3 日常操作调节325
5.1.1.4 冶炼温度的选择327
5.1.2 装料制度328
5.1.2.1 固定因素对布料的影响329
5.1.2.2 原料装入顺序329
5.1.2.3 钟式高炉装料方法329
5.1.2.4 无料钟布料330
5.1.2.5 料线333
5.1.2.6 批重335
5.1.2.7 控制合理的气流分布和装料制度的调节337
5.1.3 造渣制度338
5.1.3.1 造渣制度的要求338
5.1.3.2 对原燃料的基本要求338
5.1.3.3 一般(普通)炉渣338
5.1.3.4 特殊炉渣344
5.1.3.5 排碱348
5.1.3.6 洗炉350
5.1.4 热制度351
5.1.4.1 热制度的选择351
5.1.4.2 变料有关计算351
5.1.4.3 炉渣碱度及成分的核算352
5.1.4.4 由炼钢铁改为铸造铁的变料计算354
5.1.4.5 负荷调整356
5.1.5 冶炼制度的调整358
5.2 高压操作359
5.2.1 高压操作简况359
5.2.2 炉顶均压、放散工艺359
5.2.2.1 钟式高炉炉顶均压、放散工艺359
5.2.2.2 无料钟高炉炉顶均压、放散工艺360
5.2.3 炉顶均压制度360
5.2.3.1 两钟一室炉顶均压制度360
5.2.3.2 无料钟炉顶均压制度361
5.2.4 高压、常压转换程序361
5.2.4.1 常压转高压操作程序361
5.2.4.2 高压转常压操作程序361
5.2.5 高压操作冶炼特征361
5.2.6 高压效果362
5.2.6.1 对产量的影响363
5.2.6.2 对焦比的影响363
5.2.6.3 对生铁成分的影响363
5.2.7 高压操作364
5.2.8 故障处理364
5.3 富氧鼓风365
5.3.1 富氧鼓风工艺和设备365
5.3.2 高炉富氧鼓风冶炼特征366
5.3.3 富氧鼓风对产量、焦比的影响367
5.3.4 富氧鼓风冶炼操作368
5.3.5 高炉送、停氧操作程序(鞍钢)368
5.3.6 故障处理369
5.3.7 氧气管道维护及安全规定369
5.4 高炉喷煤369
5.4.1 高炉喷煤工艺流程布置370
5.4.1.1 高炉喷煤工艺370
5.4.1.2 制粉系统压力运行方式371
5.4.1.3 磨煤机与燃烧炉匹配方式372
5.4.1.4 喷吹罐组布置方式372
5.4.1.5 喷吹管路布置方式373
5.4.1.6 喷吹罐出粉方式374
5.4.2 高炉喷煤设备375
5.4.2.1 混合器375
5.4.2.2 分配器376
5.4.2.3 防火防爆监控技术措施377
5.4.3 高炉喷煤与停煤操作程序377
5.4.4 输煤及倒罐操作程序378
5.4.5 喷煤量调节379
5.4.6 喷煤故障及事故处理380
5.4.6.1 喷煤故障处理380
5.4.6.2 喷煤事故处理381
5.4.7 高炉喷煤防火防爆技术安全要求381
5.4.8 高炉喷煤冶炼特征384
5.4.9 高炉富氧喷煤389
5.4.9.1 国内外富氧喷吹基本情况389
5.4.9.2 富氧喷煤冶炼特征389
5.4.9.3 富氧喷煤冶炼操作390
5.5 铸造生铁冶炼392
5.5.1 铸造铁冶炼特征393
5.5.2 操作制度的选择394
5.5.3 配加硅石和炉外增硅395
5.5.3.1 入炉料配加部分硅石395
5.5.3.2 炉外增硅395
5.5.4 高纯铸造生铁395
5.6 低硅铁冶炼398
5.6.1 低硅铁冶炼发展情况398
5.6.2 冶炼低硅铁措施399
5.6.3 冶炼低硅铁的经济效益和适宜的含硅量402
5.6.4 铁水预脱硅403
5.6.4.1 向炉内喷吹脱硅剂降硅403
5.6.4.2 炉外脱硅403
5.7 炉外脱硫405
5.7.1 脱硫剂405
5.7.2 复合脱硫剂407
5.7.3 脱硫工艺408
5.7.3.1 喷吹法408
5.7.3.2 搅拌法409
5.7.3.3 浸入法410
5.7.4 宝钢铁水包镁脱硫工艺410
5.8 高炉炉况判断和调节412
5.8.1 影响炉况波动的因素412
5.8.2 正常炉况象征412
5 8.3 异常炉况象征和调节412
5.8.4 失常炉况及处理415
5.8.5 高炉事故处理425
5.8.5.1 炉缸和炉底烧穿425
5.8.5.2 水压降低或停水428
5.8.5.3 停电428
5.8.5.4 高炉停风428
6 高炉开炉与停炉、封炉与开炉、休风与送风及煤气处理429
6.1 高炉开炉与停炉429
6.1.1 高炉开炉429
6.1.1.1 开炉工艺参数控制429
6.1.1.2 高炉试水430
6.1.1.3 高炉通风试漏431
6.1.1.4 高炉烘炉432
6.1.1.5 高炉开炉配料计算434
6.1.2 高炉停炉443
6.1.2.1 停炉方法444
6.1.2.2 停炉实例451
6.2 高炉封炉与开炉454
6.2.1 高炉封炉454
6.2.2 封炉后的开炉456
6.3 高炉的休风、送风及煤气操作457
6.3.1 高炉的短期休风与送风457
6.3.2 高炉的长期休风、送风及煤气处理457
6.3.3 高炉的特殊休风465
6.3.4 特殊情况下的煤气操作468
6.3.5 煤气事故471
6.3.6 高炉煤气的净化与利用474
参考文献480
7 热风炉481
7.1 热风炉的结构形式481
7.1.1 热风炉结构形式的演变481
7.1.2 内燃式热风炉482
7.1.2.1 传统内燃式热风炉的通病482
7.1.2.2 改造型内燃式热风炉482
7.1.3 外燃式热风炉484
7.1.3.1 外燃式热风炉的结构形式484
7.1.3.2 外燃式热风炉的特征485
7.1.4 顶燃式热风炉488
7.1.4.1 顶燃式热风炉结构488
7.1.4.2 顶燃式热风炉的特征491
7.1.5 其他形式热风炉492
7.1.5.1 球式热风炉492
7.1.5.2 ZSD 型热风炉494
7.2 热风炉燃料燃烧计算与燃烧装置495
7.2.1 热风炉燃料及燃烧计算495
7.2.1.1 确定煤气成分496
7.2.1.2 煤气低发热量的计算497
7.2.1.3 空气需要量和燃烧生成物的计算497
7.2.1.4 理论燃烧温度的计算498
7.2.1.5 热风炉实际燃烧煤气量和助燃空气量的计算499
7.2.2 热风炉燃烧装置499
7.3 提高风温的措施和各种因素对风温的影响501
7.3.1 提高拱顶温度501
7.3.1.1 拱顶温度的确定501
7.3.1.2 拱顶温度、热风温度与热风炉理论燃烧温度的关系501
7.3.1.3 配用高发热量煤气提高拱顶温度502
7.3.1.4 预热助燃空气和煤气504
7.3.1.5 烧单一低发热量煤气实现1200℃以上高风温510
7.3.1.6 降低空气利用系数515
7.3.1.7 降低煤气含水量516
7.3.2 缩小炉顶温度与热风温度的差值517
7.3.2.1 增大蓄热面积和砖重517
7.3.2.2 提高废气温度518
7.3.2.3 增加换炉次数缩短工作周期519
7.3.2.4 改善热风炉的气流分布520
7.3.2.5 加强热风炉的绝热减少散热损失522
7.4 热风炉热平衡的测定和计算522
7.4.1 热风炉热平衡测定的原则523
7.4.2 热风炉热平衡和热效率的计算523
7.4.3 热风炉热平衡测定与计算实例525
7.4.3.1 测定前的准备525
7.4.3.2 测定实录526
7.4.3.3 测定数据的整理和热平衡基础参数的确定527
7.4.3.4 热平衡计算531
7.4.3.5 热效率的计算533
7.5 热风炉的操作534
7.5.1 蓄热式热风炉的传热特点534
7.5.2 热风炉的操作特点534
7.5.3 热风炉的燃烧制度535
7.5.4 热风炉的送风制度536
7.5.5 热风炉换炉操作538
7.5.6 高炉休风、送风时的热风炉操作538
7.5.7 热风炉操作全自动闭环控制539
7.5.7.1 热风炉的工作制度与控制方式539
7.5.7.2 自动控制要点539
7.5.8 热风炉的几项特殊操作541
7.5.8.1 高炉倒流休风用热风炉倒流541
7.5.8.2 扒出燃烧室掉砖541
7.6 热风炉的烘炉、保温、凉炉542
7.6.1 热风炉的烘炉542
7.6.1.1 热风炉烘炉的目的与原则542
7.6.1.2 烘炉时间与升温曲线543
7.6.1.3 烘炉方法544
7.6.1.4 烘炉实例544
7.6.2 热风炉的保温548
7.6.3 热风炉的凉炉549
7.6.3.1 高铝砖、黏土砖热风炉的凉炉549
7.6.3.2 硅砖热风炉的凉炉549
7.7 热风炉的寿命551
7.7.1 热风炉的事故及其处理551
7.7.1.1 热风炉常见事故及其处理551
7.7.1.2 热风炉的恶性事故及其预防552
7.7.2 热风炉的破损及其原因553
7.7.2.1 热风炉破损及其原因553
7.7.3 热风炉炉壳晶间应力腐蚀及预防措施555
7.8 热风炉用耐火材料556
7.8.1 热风炉用耐火材料理化性能指标556
7.8.2 蓄热室格子砖的热工特性558
7.8.2.1 格子砖的热工特性558
7.8.2.2 热工参数的计算558
7.8.2.3 常用格子砖的热工特性559
7.8.3 我国热风炉用耐火材料的进步559
参考文献561
8 炉前操作562
8.1 铁口562
8.1.1 出铁次数的确定562
8.1.2 铁口结构563
8.1.3 泥炮、开口机的机械性能564
8.1.3.1 泥炮564
8.1.3.2 开口机575
8.1.4 出铁过程监控581
8.1.4.1 出铁时间规定581
8.1.4.2 打开出铁口方法及堵铁口操作583
8.1.4.3 铁水和炉渣的流速584
8.1.5 出铁口维护585
8.1.5.1 保持正常的铁口深度585
8.1.5.2 保持正常的铁口角度586
8.1.5.3 保持正常的铁口直径586
8.1.5.4 保持铁口泥套完好587
8.1.5.5 控制好炉缸内安全渣铁量587
8.1.5.6 大型高炉出铁口维护587
8.1.6 出铁口事故处理588
8.1.7 出铁口操作考核指标590
8.1.7.1 出铁正点率590
8.1.7.2 铁口深度合格率590
8.1.7.3 出铁放风率590
8.1.7.4 铁量差591
8.2 渣口591
8.2.1 渣口结构591
8.2.2 堵渣机机械性能592
8.2.2.1 四连杆堵渣机592
8.2.2.2 折叠式堵渣机592
8.2.3 出渣过程控制593
8.2.3.1 放渣时间的确定593
8.2.3.2 放渣操作593
8.2.4 渣口维护594
8.2.5 渣口事故处理594
8.2.6 渣口操作考核指标595
8.2.7 水渣处理方式596
8.2.7.1 沉淀池法596
8.2.7.2 拉萨(RASA)法598
8.2.7.3 INBA 法598
8.2.7.4 俄罗斯炉前水渣处理系统603
8.2.7.5 轮法炉渣粒化装置605
8.2.8 冲渣水余热回收606
8.2.8.1 余热水供暖工艺流程606
8.2.8.2 系统运行参数607
8.2.8.3 余热水采暖系统热量平衡608
8.3 砂口(撇渣器)608
8.3.1 砂口结构608
8.3.1.1 结构608
8.3.1.2 砂口布置609
8.3.1.3 砂口操作610
8.3.1.4 砂口维护610
8.3.1.5 砂口事故处理610
8.3.2 出铁主沟611
8.3.2.1 主沟结构形式611
8.4 渣铁运输614
8.4.1 铁水罐及铁罐车614
8.4.1.1 对铁水罐及罐车的基本要求614
8.4.1.2 铁水罐车种类及其特点614
8.4.2 渣罐车619
8.4.2.1 对渣罐车的基本要求619
8.4.2.2 渣罐车技术性能619
8.4.3 渣铁罐周转621
8.4.3.1 铁水罐车需要量的计算621
8.4.3.2 渣罐车数量的计算622
8.4.4 渣铁罐的维护623
8.4.4.1 铁水罐的维护623
8.4.4.2 渣罐的维护625
8.4.5 渣铁罐故障处理626
8.4.6 渣铁罐运输考核627
8.5 炉前用不定形耐火材料628
8.5.1 常用不定形耐火材料理化性能628
8.5.1.1 SiO2—Al2O3系耐火原料628
8.5.1.2 石墨及碳、氮化合物632
8.5.1.3 耐火材料外加剂634
8.5.1.4 耐火材料结合剂636
8.5.2 炮泥641
8.5.2.1 炮泥理化性能641
8.5.2.2 炮泥种类及配料组成642
8.5.2.3 炮泥的制备644
8.5.2.4 炮泥的使用与管理647
8.5.3 铁沟料649
8.5.3.1 铁沟料理化性能要求649
8.5.3.2 铁沟料种类及配料组成652
8.5.3.3 铁沟料的制备658
8.5.3.4 铁沟料施工工艺660
8.5.3.5 铁沟料使用注意要点662
8.5.3.6 铁沟料质量考核663
8.5.4 铁口泥套、砂口及摆动流嘴用泥664
8.5.4.1 铁口泥套用泥664
8.5.4.2 砂口用泥667
8.5.4.3 摆动流嘴用泥667
参考文献667
9 环境保护669
9.1 国家环境政策669
9.1.1 国家环境保护法669
9.1.2 钢铁工业环境政策669
9.1.2.1 钢铁工业污染物排放标准的有关规定669
9.1.2.2 钢铁工业废水中污染物最高容许排放浓度的有关规定669
9.1.2.3 高炉煤气洗涤水循环率的规定669
9.1.3 国家噪声标准670
9.1.3.1 《中华人民共和国国家标准》中《城市区域环境噪声标准》(见表9-3)670
9.1.3.2 厂区各类地点的噪声 A 声级限制值(见表9-4)670
9.1.4 炼铁厂环境保护设计规定670
9.1.4.1 《中华人民共和国行业标准》YB 9066—95《冶金工业环境保护设计规定》中的有关规定670
9.2 环境监测671
9.2.1 噪声监测671
9.2.1.1 声级计671
9.2.1.2 滤波器671
9.2.1.3 声级分析仪672
9.2.1.4 电平记录仪672
9.2.1.5 磁带记录仪672
9.2.2 粉尘监测672
9.2.3 有害气体测定672
9.2.3.1 国家对有害气体的限值672
9.2.3.2 一氧化碳监测672
9.2.4 宝钢环境监测675
9.2.4.1 宝钢环境自动监测系统675
9.2.4.2 宝钢大气 SO2监测675
9.2.4.3 宝钢大气 NOx 测定675
9.3 粉尘治理677
9.3.1 粉尘治理设备677
9.3.1.1 袋式除尘器677
9.3.1.2 湿式除尘器680
9.3.1.3 电除尘器685
9.3.2 炼铁厂的粉尘特点及尘源密封688
9.3.2.1 炼铁厂的粉尘特性689
9.3.2.2 尘源密封690
9.3.3 出铁场粉尘治理692
9.3.3.1 出铁场除尘型式692
9.3.3.2 垂幕式除尘装置693
9.3.3.3 国外出铁场粉尘治理695
9.3.3.4 气幕式除尘装置696
9.3.3.5 湿式除尘装置698
9.3.3.6 几种出铁场除尘型式699
9.3.3.7 鞍钢11号高炉出铁场除尘700
9.3.3.8 武钢5号高炉出铁场除尘702
9.3.4 原料系统粉尘治理704
9.3.4.1 原料系统粉尘特性704
9.3.4.2 原料系统除尘抽风点的型式704
9.3.4.3 国外原料系统粉尘治理706
9.3.4.4 鞍钢11号高炉沟下除尘707
9.3.5 炼铁厂其他粉尘治理707
9.3.5.1 炉顶除尘707
9.3.5.2 铸铁机室排烟除尘708
9.3.5.3 碾泥机室粉尘治理709
9.3.5.4 铁水罐修理库粉尘治理710
9.3.6 粉尘综合利用711
9.3.6.1 宝钢工业废弃物利用状况711
9.3.6.2 国外粉尘利用情况711
9.4 污水治理712
9.4.1 煤气洗涤水治理712
9.4.1.1 煤气洗涤水特性712
9.4.1.2 煤气洗涤水治理713
9.4.1.3 沉淀池清理717
9.4.2 污泥的回收和利用719
9.4.2.1 回收污泥的工艺流程719
9.4.2.2 污泥综合利用720
9.4.3 铸铁机污水治理721
9.4.3.1 铸铁机污水特性721
9.4.3.2 铸铁机污水治理721
9.4.4 冲渣污水治理722
9.4.4.1 冲渣污水特性722
9.4.4.2 冲渣污水治理722
9.5 噪声治理722
9.5.1 消声设备型式及性能722
9.5.1.1 噪声及消声原理722
9.5.1.2 声压723
9.5.1.3 消声设备及性能723
9.5.2 冷风放风阀噪声治理725
9.5.2.1 鞍钢10号高炉冷风放风阀消声725
9.5.2.2 鞍钢5号高炉冷风放风阀消声727
9.5.3 炉顶煤气放散噪声治理727
9.5.3.1 鞍钢10号高炉炉顶煤气放散噪声治理727
9.5.4 其他环境治理727
9.5.4.1 煤粉制粉车间环境治理727
9.6 增加环保投入和加强环境治理730
9.6.1 增加环保投入730
9.6.1.1 环保投入简况730
9.6.2 宝钢环境治理731
9.6.2.1 宝刚环境治理的基本原则731
9.6.2.2 加强环保管理、增加环保投入731
9.6.2.3 宝钢环保设施的主要特点732
参考文献732
10 高炉炼铁综合计算733
10.1 原始资料733
10.1.1 必需的原始资料733
10.1.2 各种入炉物料的化学组成733
10.1.2.1 矿石733
10.1.2.2 燃料735
10.1.3 高炉报表的整理和填写735
10.1.3.1 整理记录中各项的意义及计算、填写方法735
10.1.3.2 记录要求与计算实例739
10.1.4 生产数据的核算和整理740
10.2 高炉配料计算742
10.2.1 高炉配料联合计算742
10.2.1.1 有关资料及其整理743
10.2.1.2 计算方法745
10.2.2 简易配料计算760
10.2.2.1 需加熔剂的配料计算760
10.2.2.2 不加熔剂的配料计算765
10.3 物料平衡与热平衡768
10.3.1 物料平衡768
10.3.1.1 一般物料平衡计算768
10.3.1.2 现场物料平衡计算773
10.3.2 热平衡786
10.3.2.1 第一总热平衡计算法786
10.3.2.2 第二总热平衡计算法793
10.3.2.3 高温区域热平衡797
10.4 影响高炉焦比和产量的因素800
10.4.1 炉顶高压操作的效果800
10.4.2 富氧鼓风的增产效果801
10.4.3 减风、休风影响产量的计算802
10.4.4 热风温度影响焦比的计算803
10.4.5 碱性熔剂影响焦比的计算803
10.4.6 焦炭含硫量影响焦比的计算804
10.4.7 焦炭灰分影响焦比的计算805
10.4.8 矿石含硫量影响焦比的计算806
10.4.9 矿石含铁量变化1%影响焦比的计算807
10.4.10 生铁含硅量变化0.1%影响焦比的计算808
10.4.11 一氧化碳利用率的计算809
10.4.12 氢利用率的计算810
10.4.13 高炉内还原度的计算811
1O.4.13.1 高炉直接还原度表示方法812
10.4.13.2 以 FeO 还原为基础的表示方法812
10.4.14 喷吹燃料置换比的计算814
10.4.15 影响焦比和产量的因素817
10.4.16 校正焦比822
10.4.16.1 校正焦比的方法822
10.4.16.2 计算实例822
10.5 理论最低碳比的计算824
10.5.1 计算所需条件824
10.5.2 氢还原 FeO 的还原度 ?H2824
10.5.3 作为发热剂需要碳量的两种计算824
10.5.4 作为还原剂需要的碳量计算826
10.5.5 理论最低碳比和适宜的直接还原度826
10.6 高炉操作线的计算和应用828
10.6.1 操作线作法实例828
10.6.2 操作线图的应用832
10.6.2.1 焦比潜力(△K)计算832
10.6.2.2 炉身效率833
10.6.2.3 改变炉内煤气利用率对焦比的影响833
10.6.2.4 提高热风温度的效果834
10.6.2.5 减少熔剂直接入炉的效果834
10.6.2.6 生铁含硅量变化对焦比的影响835
10.6.2.7 使用预还原炉料对焦比的影响835
10.6.3 喷吹燃料时操作线图的修正及实例836
10.7 炼铁能量平衡840
10.7.1 能量平衡方法及主要原则840
10.7.2 炼铁能量平衡842
10.7.2.1 炼铁能耗与工序能耗842
10.7.2.2 能流图845
10.7.3 合理使用能源与节能降耗851
参考文献852
附录853
热门推荐
- 2342379.html
- 3801517.html
- 1053283.html
- 2802026.html
- 2848375.html
- 1566124.html
- 1591917.html
- 1202183.html
- 1992525.html
- 1104823.html
- http://www.ickdjs.cc/book_1055269.html
- http://www.ickdjs.cc/book_1355784.html
- http://www.ickdjs.cc/book_2037195.html
- http://www.ickdjs.cc/book_1598174.html
- http://www.ickdjs.cc/book_2466327.html
- http://www.ickdjs.cc/book_1682842.html
- http://www.ickdjs.cc/book_3632018.html
- http://www.ickdjs.cc/book_2755644.html
- http://www.ickdjs.cc/book_2976575.html
- http://www.ickdjs.cc/book_2046526.html